Предприятие добилось роста эффективности проведения работ аварийно-ремонтной службы в рамках национального проекта «Производительность труда». Оптимизировать производственные процессы помогли эксперты Федерального центра компетенций (ФЦК).
Отметим, «Омскоблводопровод» вошел в число участников национального проекта в прошлом году. Предприятие обеспечивает питьевой водой жителей 13 районов области.
«Мы работали на площадке в течение 6 месяцев. Пилотным потоком для внедрения бережливых инструментов был выбран процесс по устранению подземных повреждений. Вместе с сотрудниками «Омскоблводопровода» мы изучили процесс организации аварийно-ремонтных работ, их проведения, выявили ряд проблем, связанных с логистикой, поиском инструмента и простоями бригады по причине ожидания изготовления деталей для устранения порывов», – рассказал руководитель проекта ФЦК Александр Трифонов.
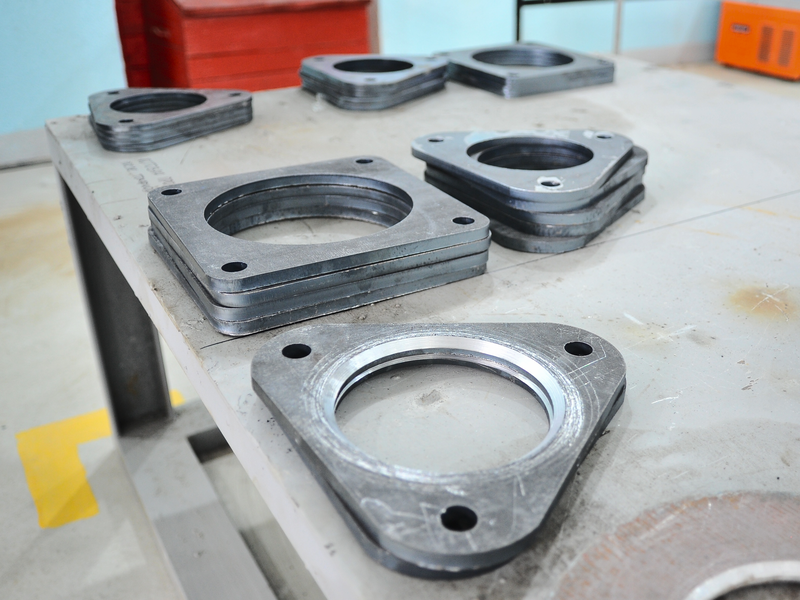
В итоге время ремонта сократили на 34%, а количество работ, которые каждый сотрудник успевает провести на участке, выросло почти в 1,5 раза. Также проработали варианты исполнения фланцев – составной части трубы, где при переходе с круглых на треугольные, значительно экономим на металле примерно на 57%.
«Мы ворвались в интересный проект, который не просто помог изменить подходы к производственным процессам, но и поменял мысли коллектива. Начали анализировать процессы и выяснили, что много времени уходит на изготовление необходимых деталей на месте порыва. На заготовку тратится 1,5-2 часа, в это время остальные члены ремонтной бригады просто ждут. А после установки бригаде нередко приходилось возвращаться к месту порыва, чтобы вновь его ремонтировать – был брак. В итоге решили организовать и оборудовать всем необходимым цех по изготовлению деталей, аварийные бригады, теперь они выезжают на ремонт уже с готовыми запчастями», – отметил Алексей Калиновский, заместитель генерального директора АО «Омскоблводопровод».
Для цеха отвели отдельное здание, организовали рабочие места для газорезчика, сварщика и токаря. Встроили в поток токарный станок, теперь рабочим не нужно бегать по разным помещениям, весь процесс происходит в одном месте. И уже сейчас удалось снизить время изготовления катушки на 26%.
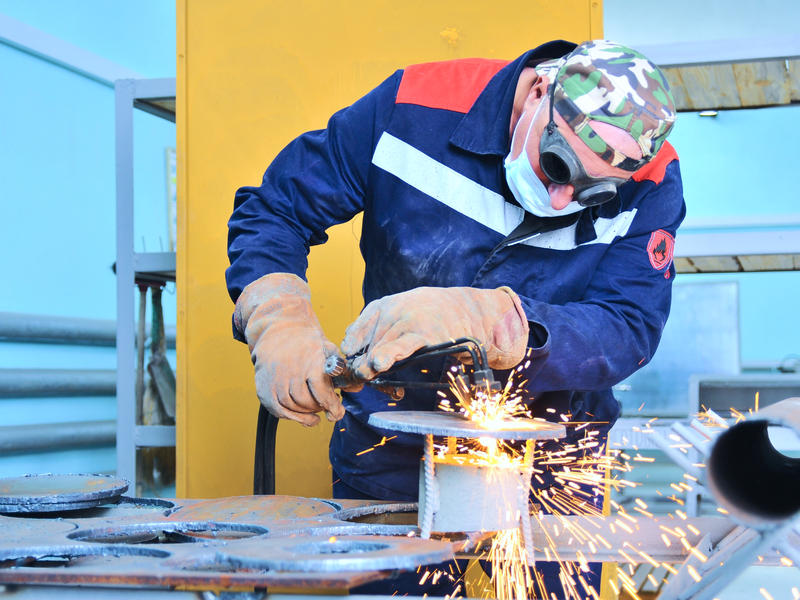
В цехе также есть возможность провести контроль качества изготовляемой продукции. В итоге это не только сокращают время ликвидации подземных порывов, но и исключают повторные протечки из-за брака. По словам гендиректора, в компании сейчас задумываются над приобретением плазменного станка для вырезки заготовок. Сейчас эта работа выполняется вручную, и требуется дополнительная работа на токарном и сверлильном оборудовании. Станок позволит оптимизировать процесс и сократить время изготовления одной заготовки.
«От того, как быстро мы устраним аварию, зависит то, насколько быстро люди получат качественную услугу – питьевую воду. – пояснил генеральный директор АО «Омскоблводопровода» Дмитрий Кремер. – Мы утвердили перечень материалов, который должен быть у ремонтной бригады. Как только у них что-то заканчивается, они дают заявку, и тогда цех начинает работать. А потом отдаем в тот район, который заказал. Больших запасов не держим, смысла нет. Есть определенное количество, которого хватает. Здесь еще важно отметить, что доставить изготовленную деталь можно на любом легковом автомобиле. Раньше, когда заготовки делали на месте порыва, нам нужно было везти еще и лист металла, трубы приходилось грузовиками направлять».
Добавим, реализация национального проекта «Производительность труда» и тиражирование опыта по внедрению улучшений в «Омскоблводопроводе» на другие процессы продолжится еще два с половиной года. Всего же в регионе к проекту присоединились 19 предприятий.