Почти тысяча российских предприятий уже стали участниками нацпроекта "Производительность труда и поддержка занятости". Одно из них — Рязанский кожевенный завод, входящий в группу компаний "Русская кожа" (крупнейший производитель натуральной кожи в России, также имеет производства за рубежом). Продукция "Русской кожи" экспортируется в 18 стран мира и применяется не только для создания обуви и сумок — она также востребована в автомобильной и авиационной промышленности, судостроении и железнодорожном транспорте. Например, в салоне российского автомобиля представительского класса Aurus используется кожа именно этого производителя.
Оптимизация по нацпроекту
Председатель совета директоров ГК "Русская кожа" Игорь Сурин рассчитывает, что благодаря участию в нацпроекте компания сможет повысить свою конкурентоспособность.
Чтобы своими глазами увидеть и оценить первые результаты повышения эффективности производства, корреспондент портала "Будущее России. Национальные проекты", оператором которого является информационное агентство ТАСС, отправилась в один из отделочных цехов Рязанского кожевенного завода, где происходит конечная обработка и получение готовой продукции.
Многие операции выполняются вручную: женщины специальными ножами обрезают края шкур, а мужчины помещают их в специальные машины для дальнейшей обработки, например, пропитки, просушки или лазерной обработки.
"То, что делается руками, обладает определенными качественными характеристиками. Почему Rolex собирается руками и почему у них точность 0,5 микрон? Это в 50 раз тоньше волоса. У нас то же самое. Кожа — это такой продукт, который полностью автоматизировать нельзя", — рассказывает заместитель директора по производству Андрей Зазерский.
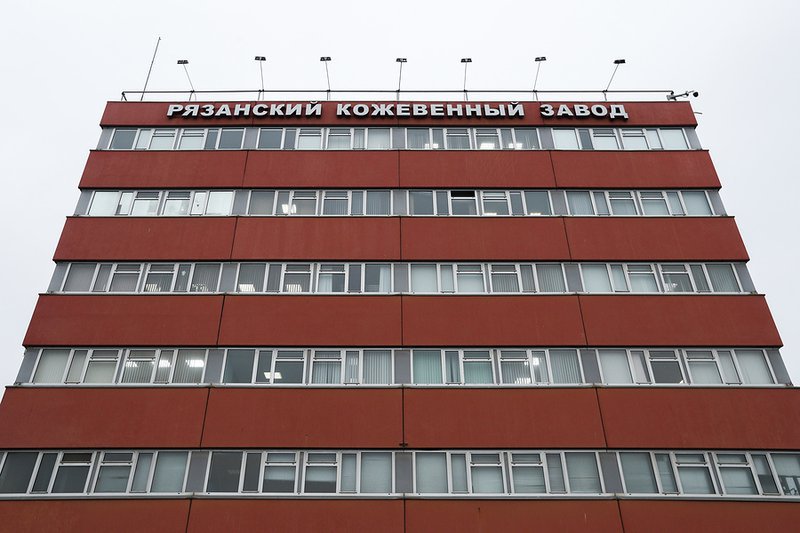
Здание кожевенного завода группы компаний "Русская кожа (Александр Рюмин/ТАСС)
На предприятии одновременно реализуются два проекта по повышению производительности труда. С первым проектом помогали эксперты Федерального центра компетенций (ФЦК) и Регионального центра компетенций (РЦК). Их задача — разработать стратегию повышения производительности на предприятии и помогать в реализации этих мер. Зазерский отмечает, что работа с внешними специалистами важна с точки зрения не только их компетенций, но и взгляда со стороны. Зачастую у работников производства замыливается взгляд, и они не замечают даже очевидных вещей.
Совместный проект с ФЦК был направлен на оптимизацию работы пресса, на котором гладится кожа. Это последняя операция, после нее идет сортировка и отгрузка готовой продукции. Особенность этого этапа заключается в том, что пресс работает в разных температурных режимах.
"Не был выстроен поток, не были применены инструменты быстрой переналадки, эффективность загрузки рабочего центра была низкой", — рассказывает замдиректора по производству.
Анализ работы показал, что при составлении планового задания следует выстраивать поток в температурном режиме. "То есть мы знаем, какая температура осталась с предыдущей смены, мы формируем плановое задание в температурных режимах либо с нижнего к верхнему, либо с верхнего к нижнему, и выстраиваем так поток", — поясняет Зазерский.
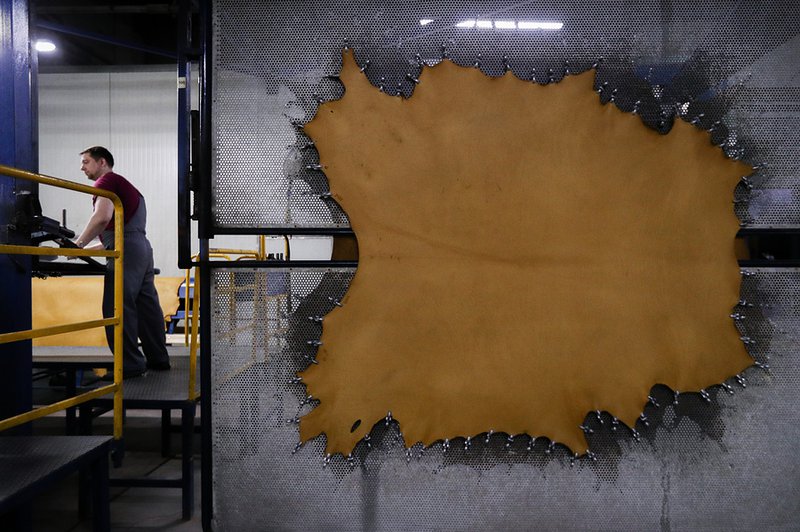
Сушка кожи на раме в цехе кожевенного завода группы компаний "Русская кожа"(Александр Рюмин/ТАСС)
Однако не всегда удается выстроить загрузку с плавным перепадом температур. Для таких случаев оптимизировали переналадку оборудования. "Бывает, что план работы на день составлен так, что нам нужно резко перейти с низкой на высокую температуру и наоборот. Реализовали инструмент, который помог сократить время на переналадку: труба с холодной водой расположена рядом с маслом, которое нагревает пресс. И поток этой воды позволил сократить время переналадки с одного часа до 25 минут", — уточняет Зазерский.
В результате удалось добиться значительного повышения производительности выбранного участка — выработка выросла с 250 до 300 штук в час.
Самому стать лидером
Второй проект по повышению производительности запустили во время обучения замдиректора по производству по программе "Лидеры производительности". Зазерский вспоминает, что поставил руководству условие — пройдет обучение, только если предприятие сразу начнет реализовывать новый проект.
Во время учебы "лидеры" делятся на команды, участники которой заняты в самых разных сферах деятельности и отвечают за различные сегменты — за производство, стратегию, сбыт или кадры. В конце обучения команды должны защитить свои реальные проекты. Команда Зазерского, которая реализовывала проект на предприятии "Русская кожа", заняла третье место.
"В команде все люди разные. Было очень тяжело выбрать тот драйвер, который может существенным образом повлиять на производительность. Мы выбрали производственный", — говорит Зазерский.
Дубильно-красильно-жировальный цех кожевенного завода группы компаний "Русская кожа" (Александр Рюмин/ТАСС)
Команда сосредоточилась на решении проблемы с логистикой внутри предприятия: разработали стандарт перемещения продукции и внедрили систему ERP (система для управления производством, трудовыми ресурсами, финансами и активами для оптимизации ресурсов предприятия).
"Банальный инструмент — штрих-кодирование, но он тоже дал свой результат. У нас теперь вся продукция перемещается по определенному стандарту, а все ее перемещения и расположение можно найти в системе. У работников на погрузчиках есть четкие схемы размещения: где что лежит и куда нужно везти ту или иную продукцию. Соответственно, когда мастер распечатывает сменное задание из системы, он видит, в каких ячейках эти партии стоят", — рассказывает Зазерский.
В дальнейшем планируется расширить возможности ERP-системы, в частности для того, чтобы работники в любой момент могли посмотреть схему расположения продукции.
Первые результаты
Пока, по словам Зазерского, не все поставленные цели еще достигнуты. "У нас стоял план сокращения времени протекания процесса (период, за который происходит обработка шкур, — прим. ред.) с 14 до 11 дней. Текущее состояние — 12 дней. Мы не достигли целевого показателя. Как идеальное состояние я себе ставлю планку восемь дней", — поясняет он.
Однако уже удалось значительно увеличить долю вовремя выполненных заказов. Раньше только 70% заказов изготавливались в срок, вспоминает замдиректора по производству. "Сейчас же мы уже на 90% укладываемся в сроки, заявленные клиенту. Конечно, оставшиеся 10% — значительная цифра с которой нам еще предстоит работать", — отмечает Зазерский.
Образцы кожи на кожевенном заводе группы компаний "Русская кожа" (Александр Рюмин/ТАСС)
Улучшать производственный процесс нужно непрерывно, уверен он: "Есть оборудование, которые мы еще не рассматривали с точки зрения эффективности. Есть цеха, которые не участвовали в пилотных проектах, — их у нас еще два, там тоже нужно провести работу. Будем успешные методы тиражировать на остальное производство".
При этом, подчеркивает Зазерский, необходимо поддерживать веру сотрудников в успех: "У меня было одно подразделение в подчинении. Они постоянно говорили: "Мы не можем, мы не можем столько делать". Обговорив некоторые пути решения с руководством, я надел рабочую одежду, вышел на производство и показал, что можно. Теперь не возникает вопросов. Теперь они говорят: "А можно еще больше".